Technology
Leader In Distributed Fiber Optic Sensing
Placing Real-time Information At Your Fingertips
Global commerce is an interconnected network of industries that rely on a continuous flow of information to effectively operate, produce, transport and protect their assets. By enriching your fiber optic network with Distributed Acoustic Sensing (DAS) technology, OptaSense puts real-time intelligence at your fingertips, making your business safer, more productive and cost effective.
Monitoring Temperature, Pressure and Strain at the Speed of Light
OptaSense DAS technology is like “The Earth’s Nervous System,” leveraging fiber optic technology to monitor the pulse of industry operations around the world.
Our technology works by converting a standard telecommunications fiber optic cable into a network of virtual sensors capable of detecting and transmitting temperatures, pressures, strain and acoustic signals along the length of the fiber, at the speed of light.
Positioned within this network is the OptaSense Interrogator Unit (IU), a highly stable laser that pulses light 10,000 times a second down the fiber optic cable. Our IU processes and records changes in the backscattered light, which indicate a function of strain on the fiber, at speeds exceeding 100 meters per second. This is called coherent optical time domain reflectometry (C-OTDR).
The position and amplitude of strain sites are determined and visualized in real time using proprietary software—providing continuous insight to optimize the decision making process for operators across a number of industry applications.
We integrate advanced optical sensing and software technologies to deliver to the customer best-in-class answer products and services.
Distributed Acoustic Sensing
Advanced distributed acoustic sensing technology delivers superior measurements for a wide range applications from advanced industrial monitoring through high performance geophysical measurements.
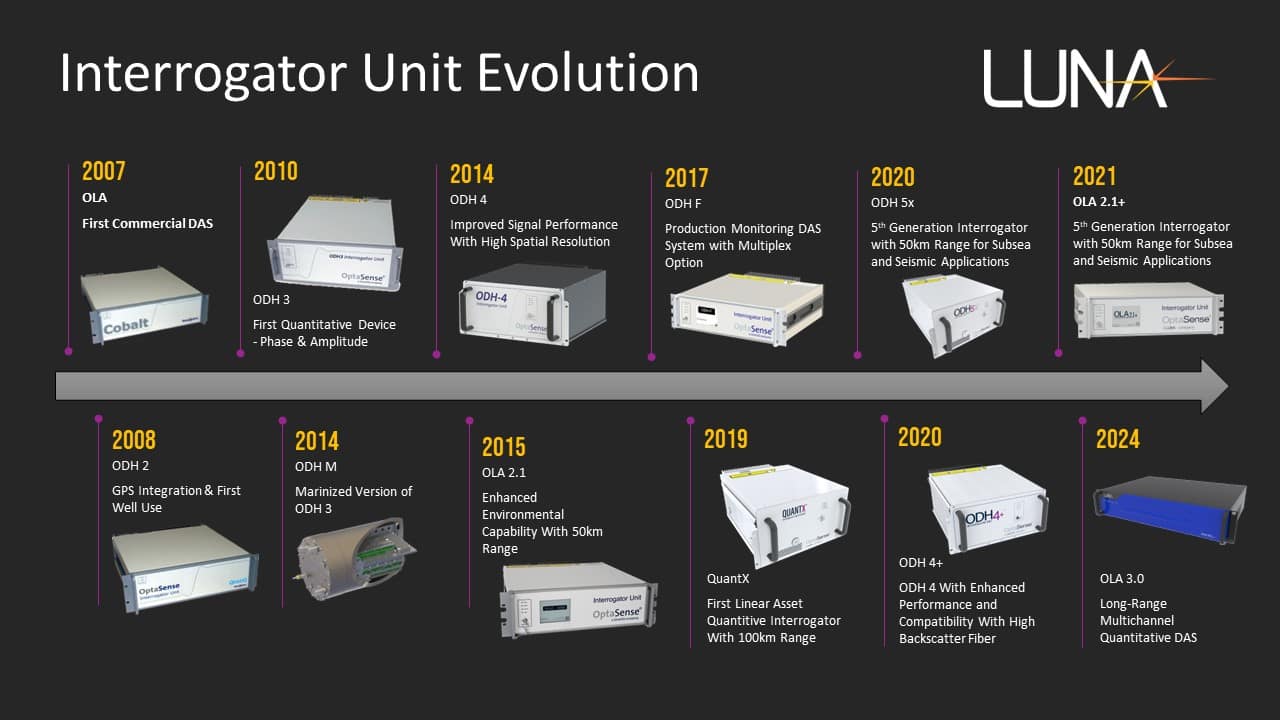
Software Platforms
Our visualization software delivers decision-ready data that promotes cost savings by increasing operational efficiency, maximizing productivity and reducing risk.
Distributed Sensing Visualization Software Platforms
OptaSense is part of Luna Innovations' portfolio of leading edge fiber optic-based solutions
Advanced Optical Technology
Luna Innovations Incorporated (www.lunainc.com) is a leader in optical technology, providing unique capabilities in high-performance, fiber optic-based, test products for the telecommunications industry and distributed fiber optic-based sensing for a multitude of industries.
In addition to OptaSense’s industry-leading Distributed Fiber Optic Sensing technology, we can also deliver advanced point-sensing with Luna’s HYPERION platform. HYPERION delivers reliable and high-performance measurement and monitoring solutions. Utilizing sensors based on Fiber Bragg Grating (FBG) or Fabry-Perot (FP) sensors, Luna’s HYPERION systems have been deployed in hundreds of challenging applications all over the world, delivering reliable, long-term monitoring with dense sensor installations.
RIO is the leading global supplier of single frequency narrow linewidth lasers, modules, and subsystems to the clean energy, security, oil and gas, and test and measurement markets.
RIO’s lasers have ultra-low noise, very narrow linewidth, unparalleled wavelength stability, small size, low power dissipation, Telecom grade lifetime reliability, at affordable prices.
Advanced Distributed Temperature Sensing
The LIOS Distributed Temperature Sensing (DTS) system monitors temperature over long distances or across large surfaces, it could be along submarine or underground power cables. Instead of installing countless numbers of conventional sensors, LIOS DTS systems use a single strand of optical fiber as sensor.
The fiber follows your installation and gives you the benefit of a continuous temperature profile in place of the more traditional single-point electrical temperature measurement.