Onshore Oilfield Services
Solutions for Unconventional Reservoirs
Onshore gas development has become a vital component of the global energy mix— but many operators developing these plays are challenged by subsurface uncertainty, higher costs and declining production levels.
Shale reservoirs are complex. Formation characteristics and production rates vary significantly across plays, wells and stages. Due to cost, advanced down hole surveillance technology is often overlooked. With limited subsurface knowledge, many shale formations are developed using factory drilling and geometric fracturing—resulting in unfavorable economics. However, cost-saving tactics, such as optimizing site selection, well spacing and stacking, fracture placement and well refracturing, are allowing operators to extract reserves at a positive net present value.
The more you know about the reservoir, the more successful you’ll be at optimizing recovery onshore
Characterize the reservoir
Once installed, the OptaSense system acts as a borehole seismic sensor array that acquires high resolution 2D, 3D and 4D VSP data. Using Distributed Acoustic Sensing (DAS) technology, this system enables operators to visualize borehole seismic data, completion operations, fracture propagation and productivity, along the entire wellbore, for the life of the asset. This insight leads to smarter well planning that optimizes development costs and enhances recovery.
Ensure successful completion operations
The system allows you to monitor the deployment of onshore completion operations in real time to ensure operational success and effective reservoir stimulation. Confirm that placement of downhole tools, such as bridge plugs and perforation guns, are in the targeted zone for optimal well performance. Confirm the seating and integrity of ball-activated bridge plugs for successful stage isolation, which is key to achieving designed fracture growth. Confirm ports are successfully opened to manage pumping execution and achieve desired placement of proppant for each stage.
Monitor fracture performance
Fracture treatments, perforation cluster efficiency and distribution of fluid and proppant can all be monitored in real time to ensure effective onshore reservoir stimulation. Quantify fluid and proppant volumes at the perforation level to identify under stimulated zones for possible diverter or re-frac applications. Monitor the distribution and placement of proppant and fluid to diagnose the effectiveness of limited entry designs and prevent under or over stimulated zones—which have a negative impact on fracture height containment, offset wells and ultimate recovery. Optimize fluid and proppant placement in real time with diversion technology, or adjust future stage perforation designs and spacing. Monitor cross well strain and temperature on a vertical monitoring well or horizontal offset treatment well for valuable insight on fracture geometry. Detect channeling outside the casing to mitigate risk in real time.
Optimize future well designs
Combined with our in-house processing and imaging services, the system can help you identify areas of the reservoir influenced by fracture stimulation to optimize future onshore well designs. Leveraging high definition 4D VSP surveys, timelapse imaging and microseismic mapping, you’ll gain a clear understanding of fracture propagation, quality and integration to improve well placement and efficiently recover reserves in large, stacked reservoirs.
Characterize induced and natural fractures by acquiring 4D time-lapse surveys, pre and post frac, to visualize subsurface regions that have been permanently affected by stimulation. This insight optimizes infill drilling operations. Understand the location, magnitude and timing of seismic events using our microseismic mapping services, to identify fracture and proppant degradation that can accelerate well declines and reduce reserves. Incorporate seismic-derived data into reservoir drainage and fracture simulation models to reduce spatial uncertainty associated with low resolution 3D seismic images. High resolution seismic images from DAS VSP can illuminate the petrophysics surrounding microseismic events.
Optimize recovery
Unlike other conventional production monitoring methods, the DFOS system lets you visualize inflow and axial flow along the entire wellbore, in real time, at the perforation level, for the life of the asset. By using an optical fiber clamped to the casing or production tubing, the DFOS system offers non intrusive data acquisition for continuous logging and on-demand surveys, without interrupting production, at a significantly lower cost compared to conventional production logging.
Pinpoint underperforming stages and clusters by monitoring production at the perforation level, across the length of the well. Correlate production flow data with geologic properties and fluid and proppant placement, to evaluate profitable field development designs. Integrate DAS and Distributed Temperature Sensing (DTS) with subsurface parameters to evaluate choke management practices and their ability to effectively drawdown across the lateral. Combine production data with 4D VSP monitoring and time-lapse imaging to monitor and evaluate the impact of production on the reservoir over time. This provides the insight to evaluate enhanced oil recovery placement and efficiency for optimal refracturing operations. Combine passive microseismic monitoring to detect induced and natural fractures for effective draw-down management. This will enhance recovery by ensuring fracture pathways remain open. Listen to production flow across artificial lift valves and pumps, providing the condition monitoring necessary to support predictive maintenance and lower lifting costs.
How It Works
The DFOS system works by transforming a standard fiber optic cable into an array of distributed acoustic sensors capable of detecting changes in pressure, temperature, stress and acoustics.
For measurement, the system utilizes an Interrogator Unit (IU), located on the surface. After injecting laser pulses down the length of the fiber, the IU processes and records changes in the back-scattered light reflection, that is a function of strain on the fiber.
The returned signal, carried by the back-scattered light, is sampled at a high frequency (up to 20 kHz). Then position and amplitude of strain sites are determined and visualized using proprietary software.
The system leverages existing permanently installed fiber, which is ideal for low cost, non-intrusive evaluation and monitoring. Once installed, it eliminates any future well interventions for repeat surveys and monitoring.
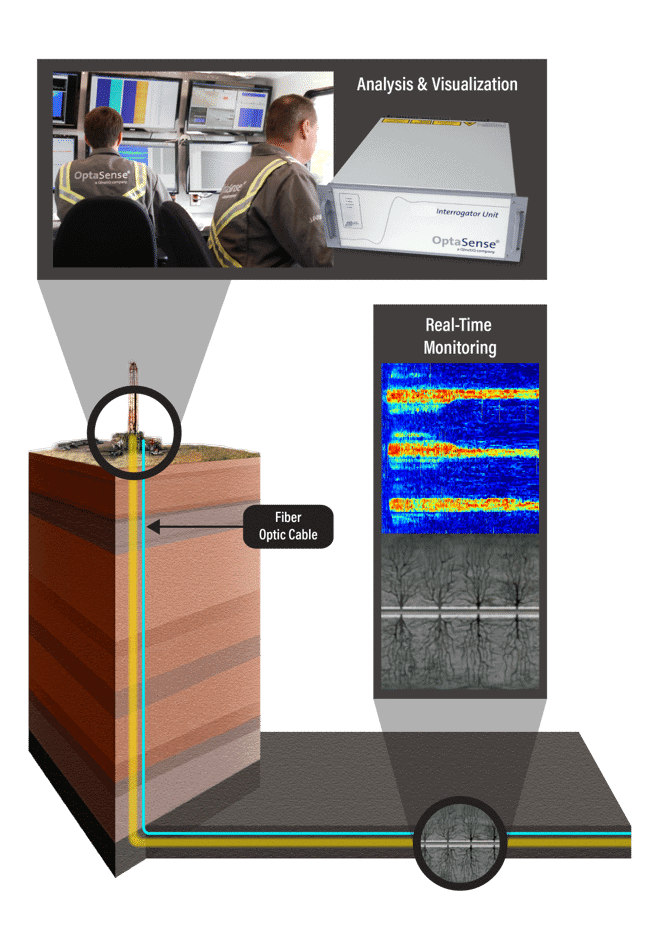