CASE STUDY
OptaSense Provides Improved Solution for Production Flow Monitoring
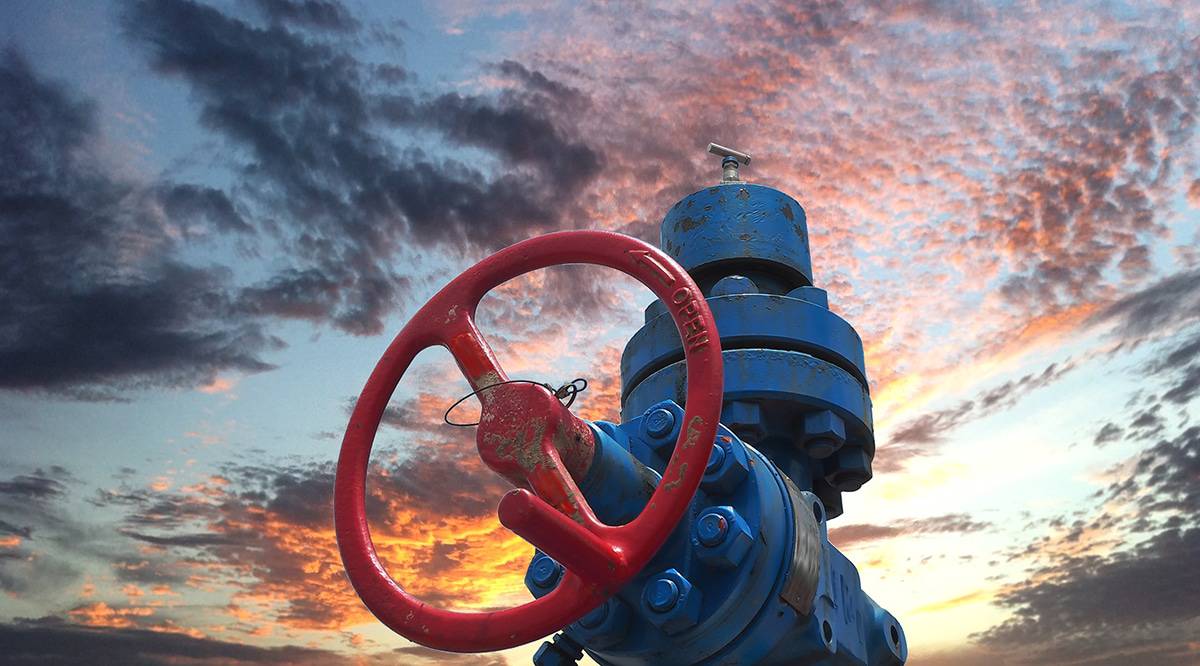
Measurement validation with existing fiber behind casing
Problem:
- Field with mix of fibered and non-fibered wellbores
- Underutilized value of permanent fiber optic cables for production flow monitoring
Solution:
- OptaSense DAS and DTS services for production flow profiling
- OptaSense’s split-flow workflow designed for permanent and conveyed fiber cables
Value Delivered:
- Maximizing utility of existing fiber cemented behind casing
- Robust production profiles from both conveyed and permanent fiber cables
- Cost-efficient production profiling for field wide campaigns with a mix of well completions
- Reduced HSE risk
The Challenge
An operator wanted to validate their process of monitoring production flow to determine if they were utilizing the most effective solution in terms of cost and data quality. To monitor production flow, the operator had been using a conveyed fiber-optic cable down inside the casing to take Distributed Acoustic Sensing (DAS) and Distributed Temperature Sensing (DTS) measurements.
A new campaign of wells selected for service already had fiber cemented behind casing, however the operator was not confident in using these fibers for production monitoring and continued to deploy a conveyed cable inside the well, submersed within the produced fluids.
The Solution
OptaSense suggested a project be conducted that included a series of production flow measurements using both the permanent fiber (cemented outside casing) and conveyed fiber to analyze the data quality and generate production profiles. The project was an opportunity for OptaSense to demonstrate that it’s Distributed Fiber Optic Sensing technology and services can be used equally in either deployed configuration.
The approach involved recording production flow simultaneously on each fiber configuration while manipulating the production on a set schedule. Analysis of the data did show that each deployment configuration produces the same production flow signals, however noise signals do express themselves differently. Most notable is the strong axial flow noise present in conveyed fiber. OptaSense’s workflows are setup for split-flow analysis to delineate axial flow and inflow signals, as well as handle other unique noise signatures found in wells.
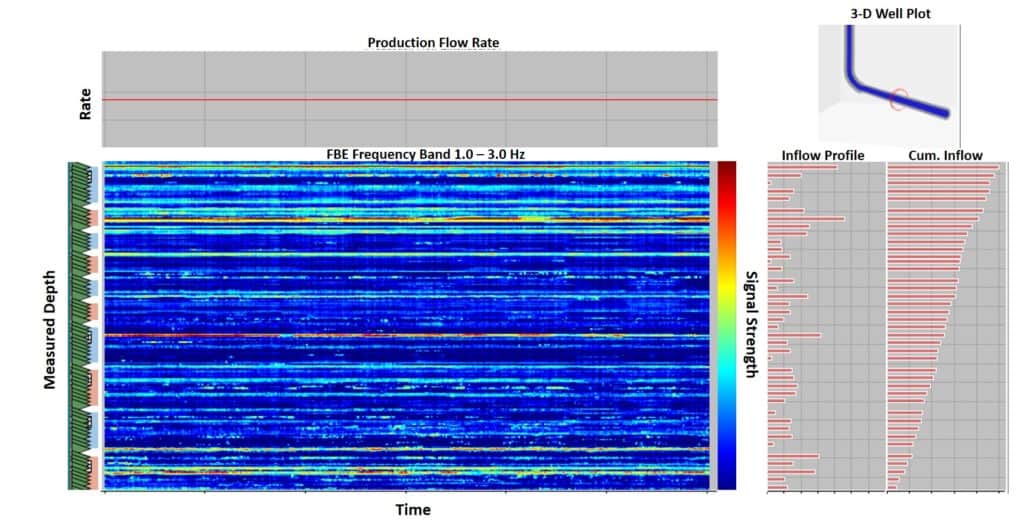
Delivered Value
Based on the results of the comparison test OptaSense was able to show that the production flow profiles and flow regime analysis from the permanent fiber was as good as the results produced from conveyed fiber. Assured of the data quality, the operator decided not to run conveyed cables in wells that are outfitted with permanent fiber. This also dramatically reduced HSE exposure on these wells.
Realizing OptaSense’s full value offering and flexibility to perform production flow measurements on either permanent or conveyed fiber has lowered the cost considerably for the oilfields with a mix of fiber and non-fiber well completions.