CASE STUDY
OptaSense Provides Enhanced Production logging for Maximized Recovery
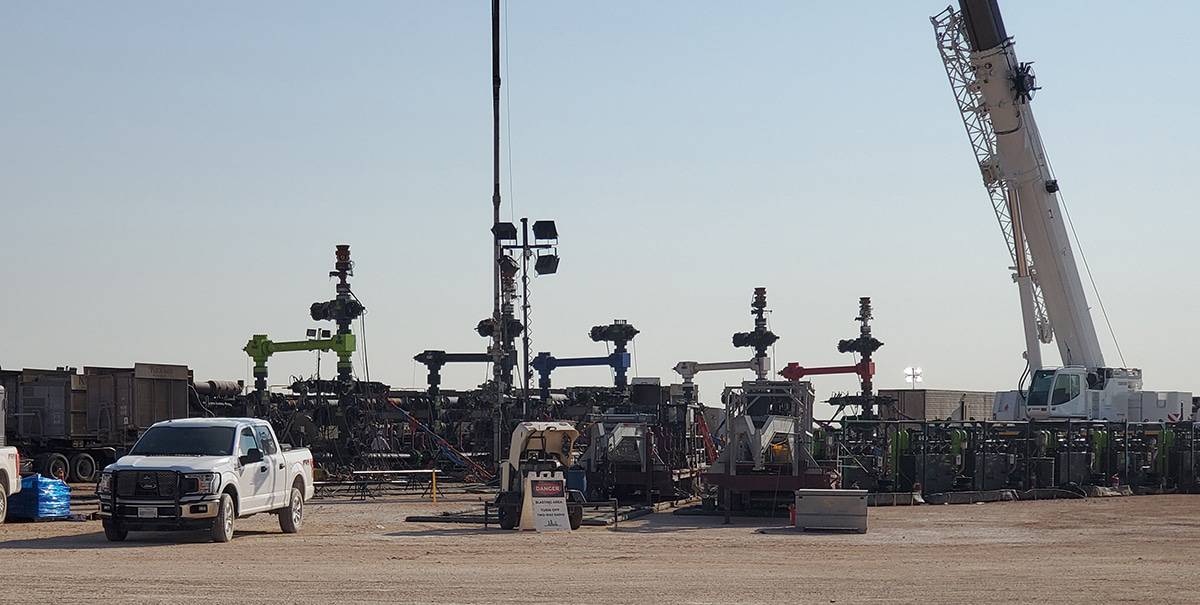
Cost-effective Alternative Results in Improved Reservoir Assessment
Problem:
- High cost of logging tools resulting in limited assessments of production
- Difficulty determining cost effective well and completion designs to maximize production
- Increased HSE risk exposure
Solution:
- OptaSense Fiber-optic Production Logging
- High resolution acoustic strain data
- Permanent continuous measurements
- Qualitative noise level thresholds
- Regime identification through frequency band analysis
Value Delivered:
- Well/field performance assessed with low-cost DFOS production logging
- Completion costs minimized by identifying optimal designs
- Oil/gas recovery and field development maximized
The Challenge
Maximizing the life and production levels in oil and gas assets requires careful well and completion design. It also requires an understanding of the interactions between the wells, the reservoir and the overall operations of the asset. With price uncertainty for oil and gas resources, it’s critical to maximize production levels while lowering operational costs and identifying well and reservoir issues before they occur so that production levels remain steady.
Identifying an optimal completion design for unconventional reservoirs, both from a cost-reducing and production maximization perspective, is the goal of completion optimization. As such it is important to know the distributed inflow profile along the entire completion, which indicates non-producing fractures, clusters of dominating production leading to premature pressure depletion, identification of natural fracture networks or nearby well connection, as well as production-hampering flow regimes or even obstructions in the well itself.
In unconventional wells, the inflow profile is rarely steady, which is induced through the intrinsic unsteady behavior of hydraulic fractures, and their repeating charge/de-charge cycle. Hence conventional, invasive tool measurements (e.g. spinner PLT) generally fail to produce repeatable results for constant surface rates.
An operator needed to assess how different completions and well designs would affect oil and gas production in an asset. The operator had to assess how much the production was changing over time and more importantly, why and where these changes were coming from. This information was critical so that future development of the field and its production could be conducted with the most efficient well designs and production practices.
The Solution
The operator deployed OptaSense’s Distributed Fiber-optic Sensing system within wells that had different completion designs. Distributed fiber-optic production logging was performed on permanently-installed fiber, which is cemented behind the casing. Its connection with the reservoir as well as with the casing enabled the identification of orifice-induced acoustic flow signatures in the completion region, while still showing regime changes and flow channel obstruction in the vertical part of the well. Fiber-optic sensing measurements, both on permanent and temporary installed fiber, provide more consistent results, as the data is collected over multiple hours or days and can hence be averaged to remove transient effects.
The magnitude of the perforation inflow acoustics was translated into a quantitative flow profile over the entire completion length. This approach can be used for one-time inflow profiling, or also applied repeatedly to examine changes in the flow profile behavior over time (e.g. at IP30, IP90, etc., see Figure 1). This knowledge hence enables the selection of more optimal completion designs or production settings.
Traditional PLT measurements are one-time occurrences that are specific to the time when they are conducted. By using permanent monitoring, the distributed fiber-optic production data revealed changes in the production and lead the operator to service or re-stimulate the wells to enhance production.
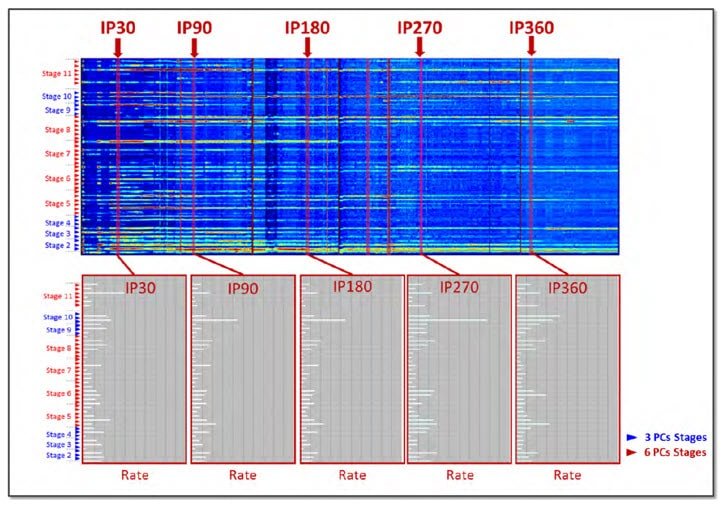
Figure 1: Waterfall plot with resulting time-lapse distributed fiber-optic production profiles
Delivered Value
Based on OptaSense’s flow production data the operator determined the optimal well design that provided the highest oil/gas production. A producing well in an unconventional reservoir was completed with two different cluster densities in a plug-and-perf completion design (3- vs. 6-clusters per stage) to examine the treatment distribution effectiveness of the hydraulic fractures. Fiber-optic production logging was performed on the permanently installed fiber, and the acoustic based inflow profile along the completion section was determined for an extended production period. The ability to monitor the well permanently and stream the data for analysis allowed the operator to have continuous flow measurements without disrupting the well dynamics. This further reduced the intervention costs.
The results revealed that the 3-cluster fracture design was producing more uniformly and hence provided better oil recovery, both daily, as well as over the examined 2-year time period (see Figure 2). This allowed for the implementation of the better 3-cluster completion design in subsequent wells, hence providing maximized individual well production and minimizing the associated completion costs of the field development. The use of the permanent monitoring flow data further enabled the operator to intervene in the well/field operations to enhance production in instances where flow rates decreased in certain locations.
Using OptaSense’s fiber optic technologies, the operator has been able to demonstrate that they can monitor their wells remotely, greatly reducing HSE exposures.
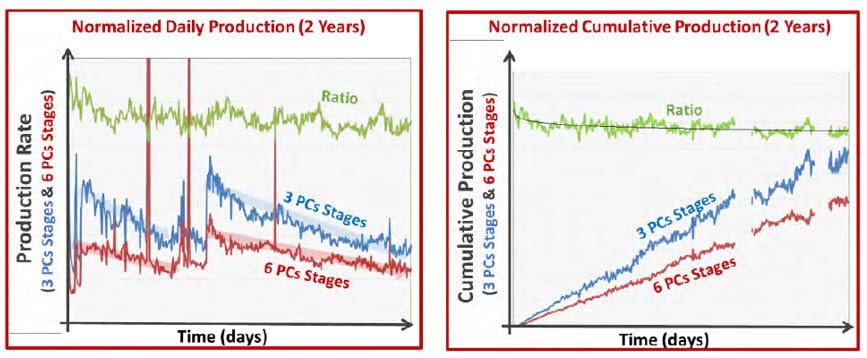
Figure 2: Daily and cumulative production determination via fiber-optic production logging.
For more information, please contact your OptaSense representative or visit optasense.com/oilfield-services/production-monitoring/